More Thoughts on Galvanic Corrosion for Aluminium Yachts
This article follows our earlier post on Aluminium Catamarans.
What is Galvanic Corrosion?
Galvanic corrosion occurs when two dissimilar metals come into electrical contact in the presence of an electrolyte, such as saltwater. This process creates a galvanic cell, where one metal (the anode) corrodes faster while the other (the cathode) is protected. Aluminium, when paired with more noble metals like stainless steel, becomes the sacrificial anode, corroding more rapidly in this environment.
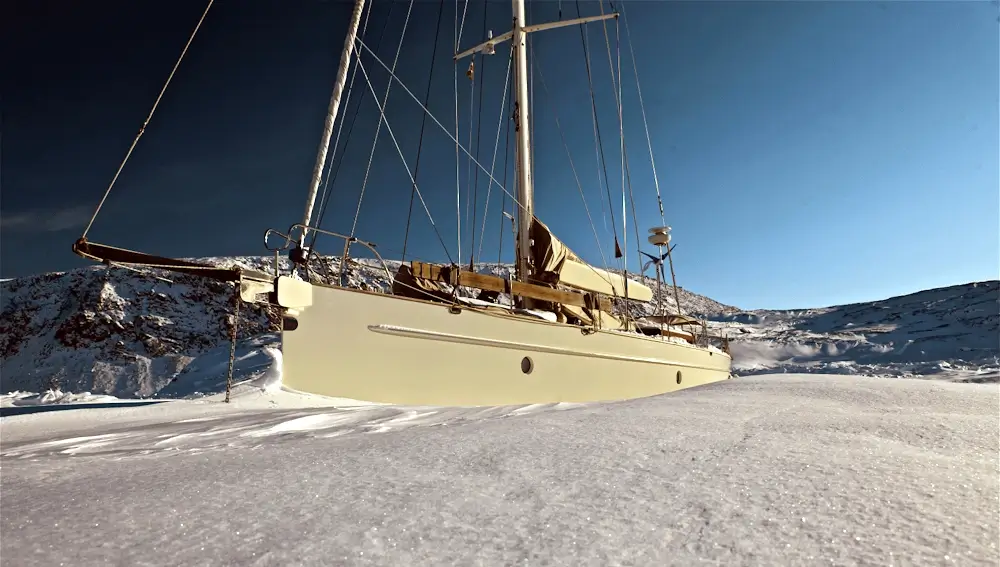
Why is Aluminium Susceptible?
Aluminium’s reactive nature makes it susceptible to galvanic corrosion when improperly protected. In a harsh marine environment, especially in marinas where boats are docked closely, stray electrical currents and exposure to saltwater can exacerbate the issue. Factors that increase the risk include:
- Contact with Dissimilar Metals: Stainless steel fittings, bolts, or even props can trigger galvanic reactions with the aluminium hull if not properly insulated.
- Stray Electrical Currents: Poorly designed or faulty electrical systems in marinas can cause stray currents that accelerate corrosion on aluminium boats.
- Electrolyte Presence: Saltwater acts as an excellent electrolyte, increasing the rate of corrosion.
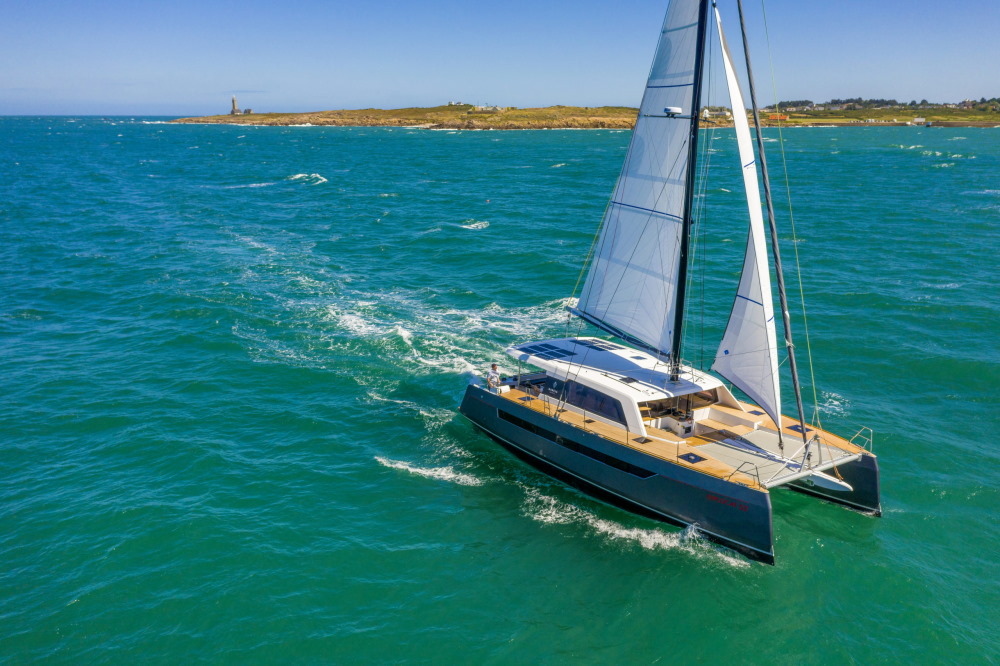
Galvanic Corrosion in Marinas
Marinas present a challenging environment for aluminium yachts due to:
- Shared Electrical Systems: Power supplies in marinas often leak small amounts of stray current into the water, amplifying corrosion risks for aluminium boats.
- Close Proximity to Other Boats: Nearby boats with mixed materials or poorly grounded systems can increase galvanic activity.
- Saltwater Conditions: Constant immersion in saline water accelerates the corrosion process if preventative measures aren’t in place.
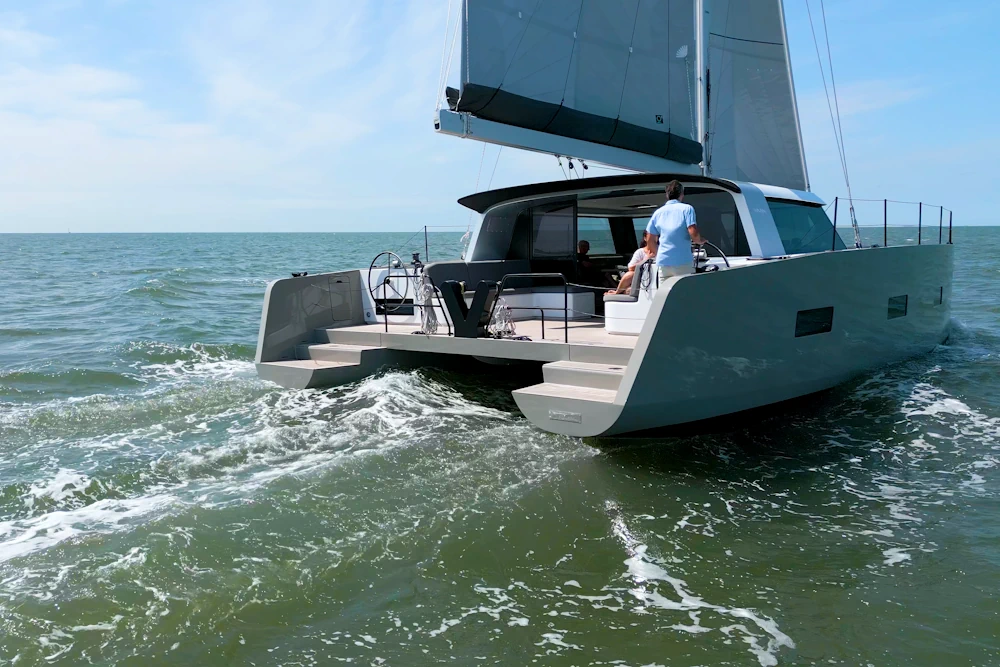
Preventing Galvanic Corrosion
Aluminium yachts can be protected through several strategies:
- Proper Insulation: Use non-metallic gaskets or insulating sleeves between aluminium and dissimilar metals to prevent direct contact.
- Sacrificial Anodes: Attach zinc or magnesium anodes to the aluminium hull. These anodes corrode preferentially, protecting the aluminium.
- Protective Coatings: Apply marine-grade paint or anodizing to create a barrier between the aluminium and seawater.
- Electrical Isolation: Ensure the yacht’s electrical system is well-grounded and insulated. Using galvanic isolators or cathodic protection systems can help mitigate stray current issues.
- Regular Maintenance: Frequent inspections of the hull, anodes, and fittings can catch early signs of corrosion and prevent major damage.
Understanding and addressing galvanic corrosion is critical for owners of aluminium yachts, particularly those who spend significant time in marinas. By adopting these preventative measures, the longevity and performance of aluminium hulls can be preserved, even in challenging environments.
Note that there is a silver lining here. Aluminium will form its own oxide layer and can just be kept natural (or brushed). You will need to paint for antifoul and for aesthetic reasons, but many owners go for stickers/wraps.
As with yachts built in any material, the key here is regular inspection and maintenance. If properly looked after, aluminium yachts will last 40 years or more and they can be recycled at the end of their life.